3D printing technology is revolutionizing the automotive industry, particularly in the realm of high-performance vehicles. This innovative technique allows manufacturers to create complex, lightweight, and highly efficient components that were previously impossible or impractical to produce using traditional methods.
One prime example is Bugatti’s new 1,800 hp Tourbillon. While the exterior design may appear similar to its predecessor, the underlying technology is groundbreaking. Key components like suspension arms and linkages are 3D-printed, resulting in a significant weight reduction and optimized performance.
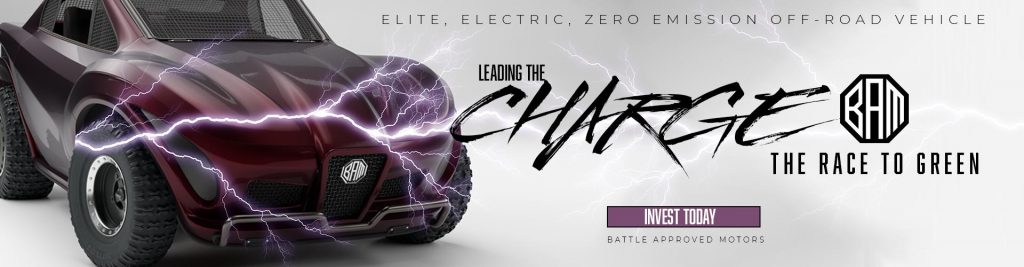
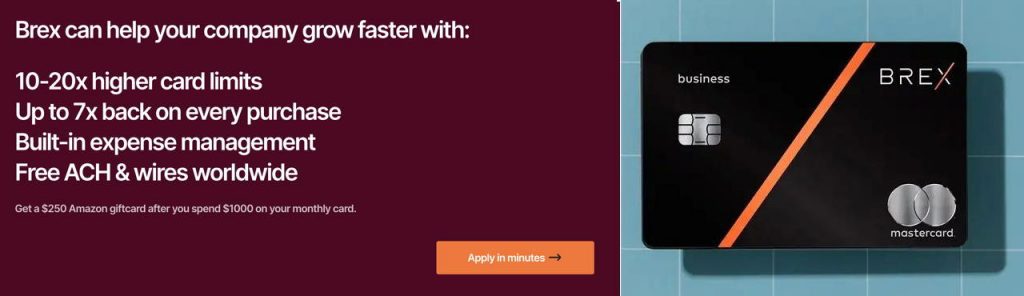
Czinger, another prominent player in the hypercar segment, has extensively utilized 3D printing in its 1,350 hp 21C. The company’s expertise in this technology even led to a collaboration with Bugatti on the Tourbillon project.
Read More: Extreme H Signs 3-Year FOX Sports Deal
Auto Giants Embrace 3D Printing for Performance and Efficiency
Even larger automakers like General Motors and Porsche are embracing 3D printing for various applications. GM has used this technology to rapidly produce replacement parts, while Porsche has explored its potential for performance enhancements, such as 3D-printed pistons and seats.
While 3D printing offers numerous advantages, it’s important to note that it’s currently best suited for low-volume, high-performance applications. The upfront costs and potential limitations in terms of fit and finish can be significant. However, as the technology continues to evolve, it is expected to become more affordable and accessible, expanding its applications in the automotive industry.