Shima Seiki’s automated knitting machines make quick, whirring noises in the open studio of a remodeled 36,000-square-foot factory in Los Angeles’ Chinatown. Around the machines, automated guided vehicles move things like spools of yarn in all the colors of a Crayola box, while robot arms work on the uppers and outsoles of the shoes as they roll down the conveyor lines.
Teams are crowded around computers, talking about design plans in a lively way. This is the headquarters of KX Lab, a brand-new factory that makes mostly automated knit sneakers in the middle of one of the most important urban sprawls in the United States.
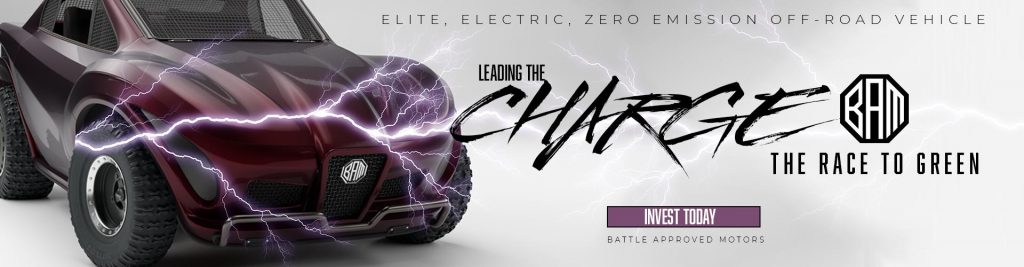
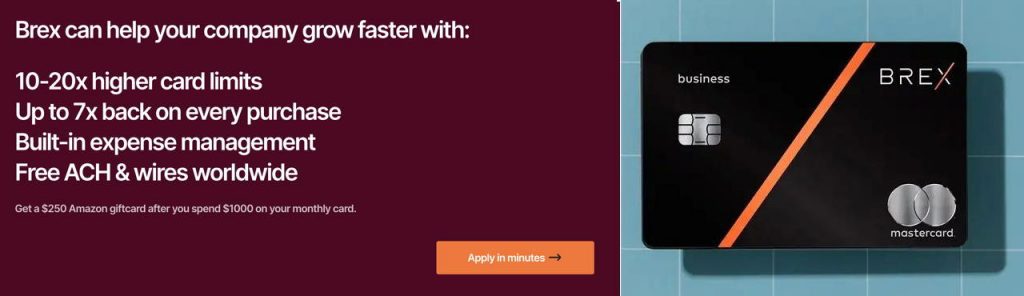
When you look at the bottom of your sneakers these days, it doesn’t say “Made in the USA” very often. Even though the US is the biggest importer of shoes in the world (it got about 2.4 billion pairs in 2021), it is usually not where shoes are made. In 2021, China, India, Vietnam, and Indonesia made almost 75% of all the shoes in the world. (China is number one by a long shot, making more than 12 billion pairs last year. India was number two, making 2.6 billion pairs.) The reason is clear: making shoes in Asia is cheaper than making them almost anywhere else, but especially in the United States.
Shoes are made in the US, but on a much smaller scale than in other countries. Last year, New Balance opened its fifth U.S. factory in Massachusetts. It is an 80,000-square-foot building.
But a price comparison on New Balance’s website shows that a pair of Made in the USA sneakers starts at $184.99, while a pair of sneakers whose origin is unknown could start as low as $64.99. This is because New Balance still gets parts for many of its shoes from overseas. Price is affected by many things, but making shoes in the United States is definitely much more expensive.
So when Joshua Katz opened KX Lab, he wasn’t thinking about saving money. Instead, he was thinking about being green and working together creatively. Katz says that the goal of the lab is to bring the “product-creation engine” closer to both the people who make things and the people who buy them.
“If you can work with the factory down the street, you can make smaller batches, be closer to sampling and development, and bring products to market on a smaller scale,” he says, adding that this reduces carbon emissions that would otherwise come from shipping goods around the world. But Katz also sees an important chance for brands to be much more involved in the creative process and maybe be inspired to take more risks.
In Asia, automated knitting has been used to make sneakers for years, but in the West, it is still a relatively new way to make shoes. And to get brands on board, KX Lab was built “like a prototype facility in the sense that here we can experiment, learn, and improve,” says Katz. He adds that the lab is always changing to find out how to knit fabrication can be more useful to the American design industry.
Shima Seiki’s automated knitting machines, which are the industry standard for knit shoes, can make whole sneaker uppers in just 25 minutes. The Shima Seiki takes the upper designs and knits the whole thing. Reinforcement parts are made with machines that use laser cutting. The goal is to reduce waste and physical work as much as possible.
Clae, a company based in Los Angeles that has been making minimalist sneakers with classic shapes since 2001, released its first made-in-the-USA style with KX Lab at the end of last year. The Louie is a lifestyle sneaker that looks like a running shoe but wasn’t made for running. It has Clae’s signature sleek look and more technical features, like a variety of knitting styles that are tight where you want them to be, like a snug collar that wraps comfortably around the ankle, and looser where you want more airflow.
Some people’s jaws also dropped when they saw the technology, especially when the Clae team saw robotic arms (like those used by car manufacturers) putting glue on the soles and uppers to connect them. Clae has also been concerned with sustainability for a long time. For example, it makes sure that its factories in Vietnam pay fair wages and works with tanneries in Mexico to make cactus-leather sneakers. The team likes how laser-cutting technology is used in knit manufacturing to reduce waste. Also, a single-piece printout doesn’t need any glue.
Clae CEO Jim Bartholet says, “We priced this shoe less than we usually do, but that was because of how simple the design is and how that affects how much it costs and how much it seems to be worth.” “We also wanted it to be easy for people to use.” Because the Louie was made in a limited run that wasn’t always cost-effective, the brand decided to stop selling it in stores and sell it only through Clae.
Because of the cost of getting started, Clae used a mix-and-match approach to sourcing when it started making things in the United States. The knit upper was made in its entirety in KX Lab, while the outsoles, laces, and insoles were made in Vietnam by factories with which KX already worked. But if you look at all of Clae’s sneakers, the Louie, which costs $180 per pair, is on the high end of the price range.
Bartholet, on the other hand, says that because KX Lab’s automated manufacturing process requires less work, a larger order could help bring the price down. Even so, the benefits of making a shoe locally still outweigh the extra cost. Ji-San Lee, who is a senior designer at Clae, agrees that being close was a game-changer.
Clae shoes are usually made in other countries (its last knit low-tops were made in Vietnam), so why would they have a factory an hour away from their headquarters? That changes everything a lot. “In modern design, it’s easy to just send off your work and hope that the developer or pattern maker understands it correctly,” Lee says. “So it was a breath of fresh air to be able to sit down with other creatives and find workarounds or solutions whenever we hit a snag in the design process.”
Katz knows that people want to know how their stuff is made, just like they want their food to be more environmentally friendly. “The opaque black box of how and where things are made has already given way to a more open process of making things,” he says. “And that can be just as important as the actual materials.” The shoe brands that make shoes at KX Labs want to take advantage of this rising interest.
KX Lab has only been around for a little over a year, and most of the things it has made are sneakers. Katz is sure that there is a lot more that can be done, though. The KX team is looking into how automated knitting could be used in the clothing, home goods, and car industries. Katz says that he wants them to push the limits of how they can use existing technology, like thermoforming fuse yarns, and to look into how it can be used with other production methods, like 3D printing.
“One of the hardest places to make things is in Los Angeles,” he says. “There are strict rules about the environment.” Since living costs are high, so is the cost of labor. But we said, “If we can do it here, we probably can do it anywhere.”